Imagine having a sample of the object you want to make. Everything about it looks great, feels right, and like it was meant to be. That moment doesn’t just happen; it’s brought to life with a unique method called vacuum casting. You can use vacuum casting to turn your ideas into real things, whether you’re a business with a big idea or an artist who wants to make their ideas come to life. Let’s look at how this interesting method turns ideas from rough sketches on paper into real things that can be tried, touched, and improved.
How the Vacuum Casting Process Works
A master model, which is usually made of metal or plastic, is the first step in vacuum casting. Vacuum Casting was made with great care to show every feature of your design.
The master is then covered in silicone rubber to make a mould. Any mistakes in this step can affect the end result, so it needs to be done carefully and with skill. The mould is taken off the master once it is dry.
When polyurethane or another casting material is put into this mould while it is vacuum-packed, magic happens. The hoover gets rid of air bubbles that could damage the surface.
You can take off the plastic mould to see your cast part after letting it set. This method makes it possible to make many high-quality samples at a much lower cost than standard production. Each piece shows fine features and exactly what was asked for, so it’s ready for testing or production.
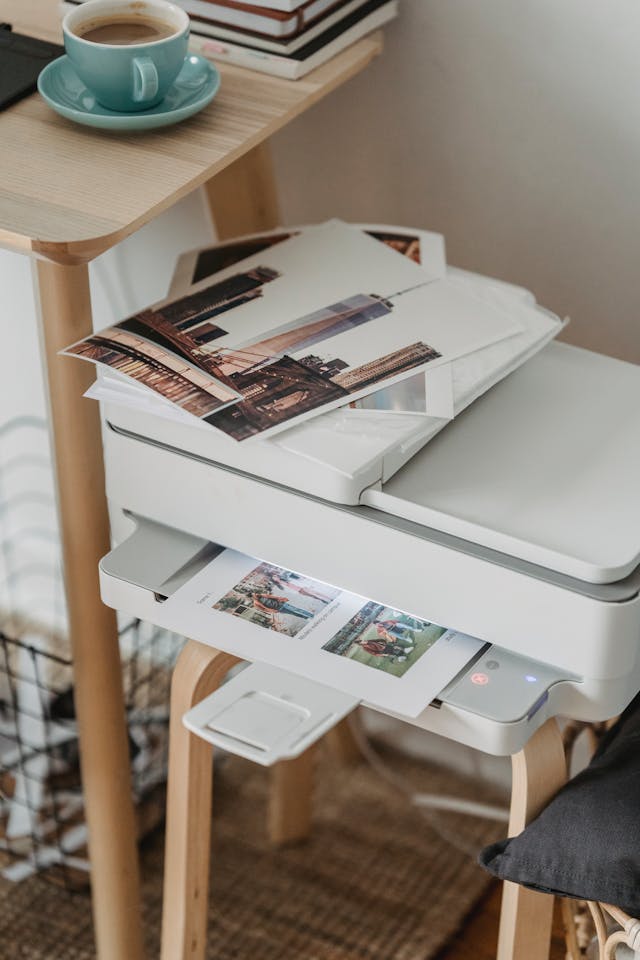
Why vacuum casting is a good idea
For prototypes and small batches, vacuum casting is the best way to go because it has so many great benefits. Precision is one of the best things about it. The process makes sure that every mould has a lot of detail, so even complicated patterns are easy to capture.
Another big benefit is that the material is flexible. You can pick from many materials, like thermoplastics and silicone rubbers, so you can make solutions that fit the needs of your project.
Cost-effectiveness is also very important. When compared to standard ways of making things, vacuum casting needs less money up front and can make things quickly. It’s perfect for new businesses or projects that don’t have a lot of money.
Another good thing is that it cuts down on waste. By only using what is needed during the casting process, this method cuts down on the waste of material. Not only does this save resources, it also encourages environmentally friendly practices in fields that want to be sustainable.
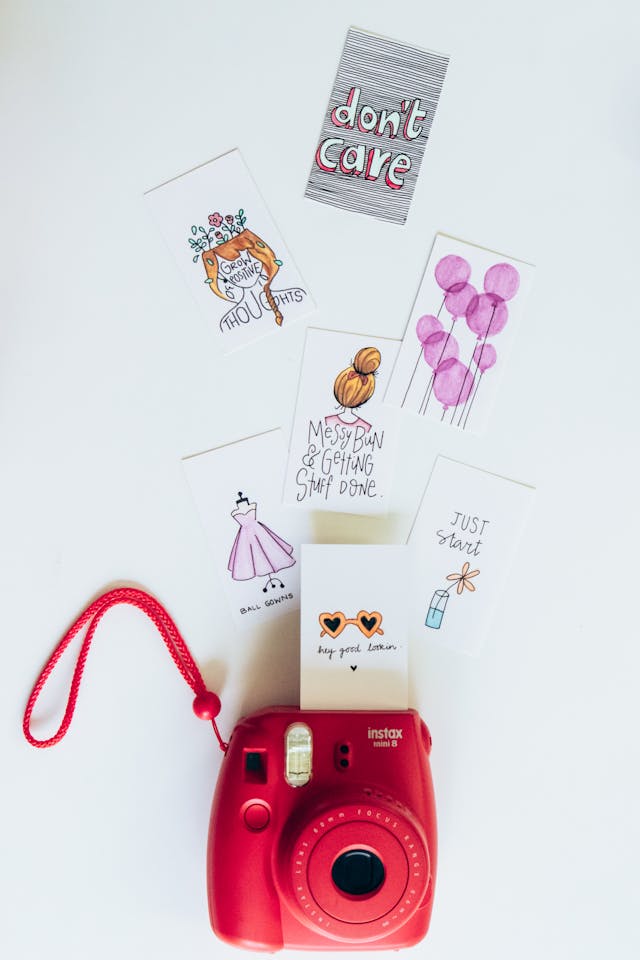
Vacuum casting is used in many different industries.
The fact that vacuum casting is used in many fields makes it a very useful method. It is used in the car industry to make prototypes and parts that are very complicated and need to be very precise. So, ideas can be tried before they are made in large quantities.
Vascular casting is also very useful in the medical area. Custom surgery tools and parts are made with great accuracy, which improves the results for patients.
This method is also used in electronics; the cases and housings for devices are made to meet strict requirements while still being durable.
Companies that make consumer goods use vacuum casting to make one-of-a-kind patterns at lower costs. This lets new ideas come up without slowing things down or lowering the quality.
Even the aircraft industry uses its benefits by making parts that are strong but not too heavy, which are important for flying operations’ performance and safety.
Vacuum casting is a popular choice in many fields because it can be used for so many different things.