Access equipment are used in many industries and some examples are boom lifts, scissor lifts and cherry pickers. You need to know how to hire the right access equipment for your purpose and to ensure safety in your project.
Consider what your needs are when it comes to access equipment hire. You have to think about the type of project you are working on and the nature of the working environment. There will be certain requirements for height. Think about the height you want to reach to carry out the project. This will help you select the right equipment for the job. You have to select a reputed supplier for the access equipment and this can be done by searching online for such companies and checking customer reviews and ratings.
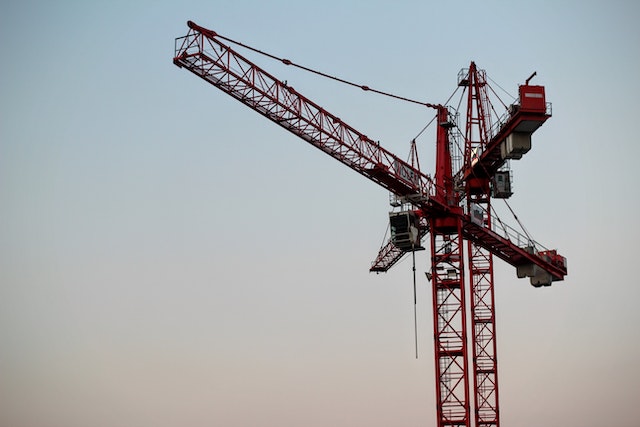
You can also ask for recommendations from colleagues. When choosing a company, the supplier as well as the equipment should be fully licensed and insured. This ensures their commitment to keeping up with local regulations and standards for safety. You need to have proper certification and training when operating access equipment. You can ask whether the supplier can also provide experienced operators if that is the requirement.
There are different types of access equipment
So you have to research the options available for your job. Make sure to check the pros and cons of each equipment so that you are able to choose the right one for the project. You can also present your requirements to the supplier so that they can make some recommendations. Before you finalise the hiring process, it is important to inspect the equipment to get a good idea of its condition.
There should not be any damage to the equipment and they should be well maintained. Ask about the safety features of the equipment such as attachment points for harnesses and guardrails. You have to ask the supplier about the age of the equipment and the history for maintenance. By selecting newer equipment, you have a benefit as these will have the latest safety features. These also tend to have better fuel efficiency.
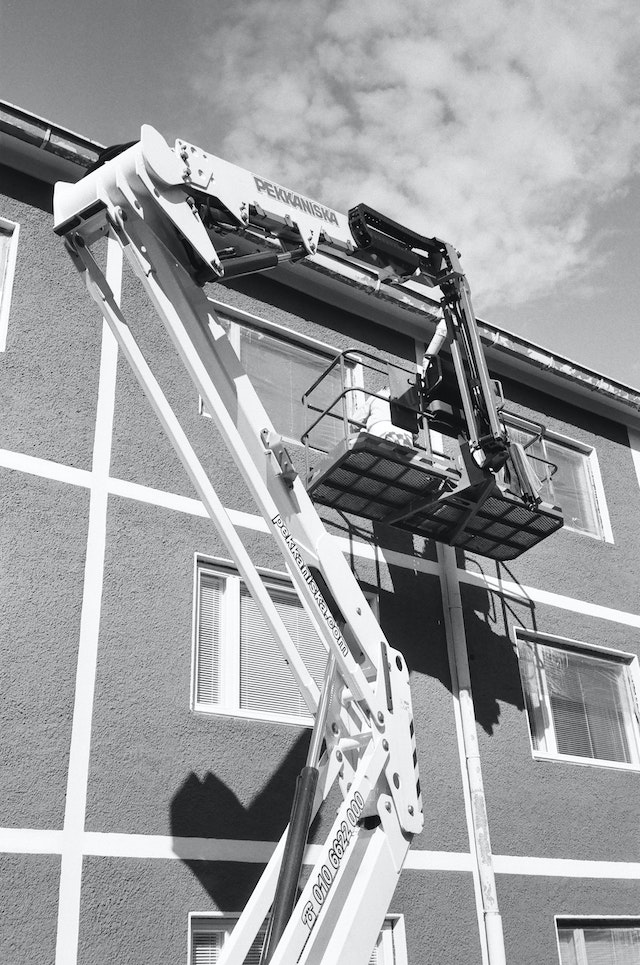
By asking
To see maintenance history, you can get an idea about the condition of the equipment. This allows you to choose equipment that will come with a high level of functionality. This is a great way to minimise issues during the project and reduce downtime. However, ask about the process in place if the equipment is to malfunction; the supplier should be able to provide you with a replacement within an acceptable time.
Sometimes your team will not be experienced in operating the equipment. In this case, you can ask the supplier whether they offer training options. This will ensure safety and efficiency of the project. Ask to see proof of insurance so that you have a better idea of the insurance coverage for the equipment. You should also check how the logistics will be handled. This will clarify the party responsible for the transport of the equipment. If the supplier is delivering the equipment, you need to ask about associated costs.